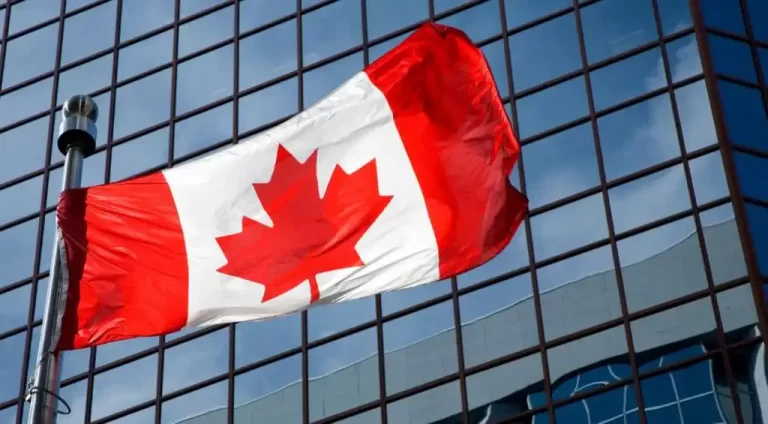
Advanced Technologies in Design, Furniture, and Marketing
In industries like design, furniture manufacturing, and marketing, staying competitive means delivering high-quality products quickly and efficiently – all while keeping costs in check. As demand for customization and faster time-to-market grows, technology has become a critical enabler. From automating repetitive tasks to creating larger-scale prototypes, tools like DriveWorks, SOLIDWORKS, and BigRep 3D printers, empower businesses to innovate while optimizing production processes.
Let’s explore how these technologies can help Canadian companies in these industries reduce costs, improve workflows, and get products to market faster.